How to Build Supply Chains Resilient to Global Disruption
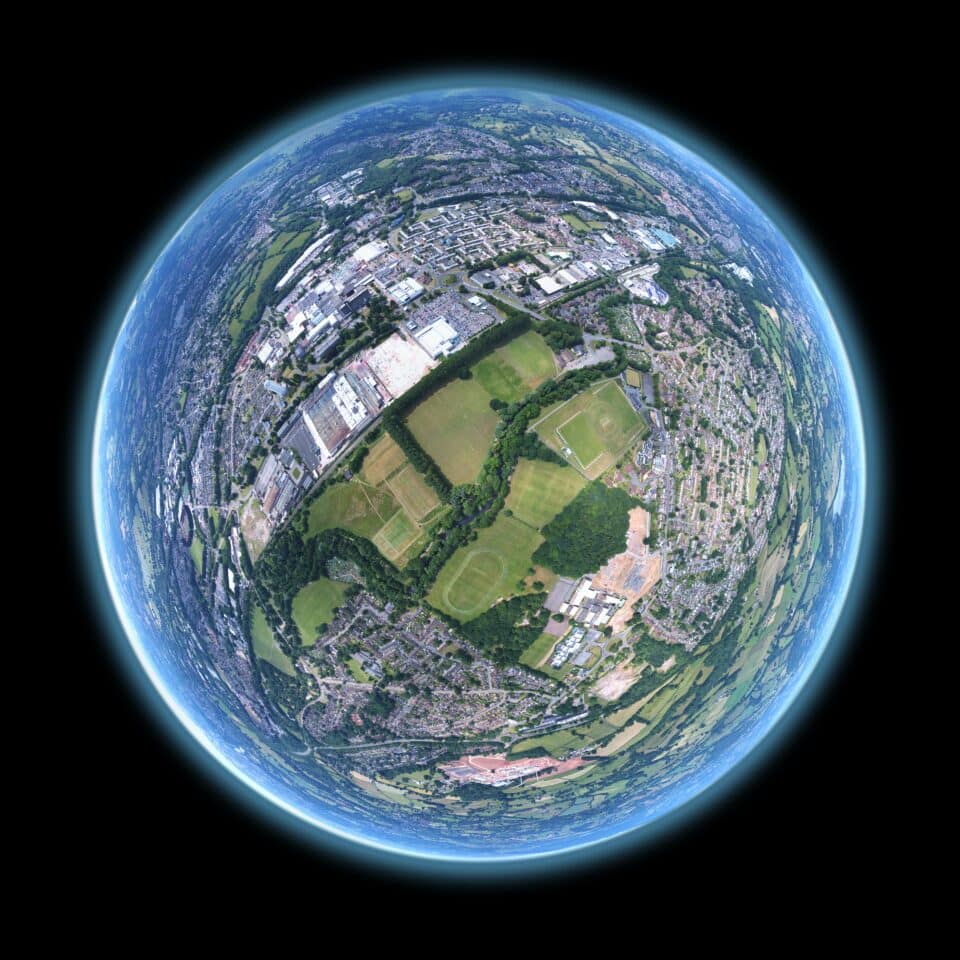
Jake Rheude of Red Stag Fulfillment shares some top tips on building a resilient supply chain.
No part of a global supply chain has been left unchanged during 2020. The industry has long spoken of how supply chains are connected and operate in tandem, but we got a much closer look as elements broke down, delays stretched on. Many realized they lacked the proper mix of capability and planning to tackle times when lean supply chain methodology created risk.
Recovery is a challenging prospect but possible for nearly every chain still. The question is how to get things back to an operational status that also provides long-term security. Resilience is the word of the quarter, resting on all lips as supply chain risk assessments are finished and critical gaps identified.
Leaders will soon build action plans based on situational analysis and large-scale test scenarios related to this and other disasters. Getting it right comes with core elements, and most discussions focus on diversification of partners and physical locations. Looking beyond that, we see some structural elements for supply chains that can support resilience in the near-term and as they grow.
Invest in collaboration
COVID-19 highlighted that many global supply chains operated as a series of smaller chains connected at different points. Siloed data meant most could look upstream, only one or two tiers. Everyone expected things to run smoothly.
When expectations were dashed, we discovered that supply chain decisions and issues many tiers above had compounding effects that led to downstream delays. As these delays impacted orders and demand, the ripple went in the other direction and harmed back up through production and raw materials suppliers. The companies that avoided this had supply chains already sharing data and collaborating on information and alerts to understand changes at any given point and moment.
Resilience demands real-time data. Global brands should begin to invest in supply chain AI and machine learning that looks for gaps in information and shifting patterns — from production through consumer spending — to identify bottlenecks as well as disruptions. Being a partner that provides information and highlights issues early makes you a powerful ally in responding to concerns. It protects your business and your partners, making them more likely to place your interest first when push comes to shove.
Forecast solutions that include virtual models and representations of your supply chain can help you best understand scenarios and test responses in as close to real-time as possible, giving you your best chance to make the right call.
Secure warehousing early
To put it bluntly, COVID-19 kicked supply and demand in the teeth. We’ve seen it across commodities, products, sectors, and localities. One of the more significant impacts has been strengthening the warehouse sector as companies fought for space and partnerships, even if they couldn’t necessarily move their foods.
The spike in e-commerce and other pre-COVID trends have put warehousing in a stronger position than at any other point in recent memory. Demand is up significantly compared to recent years, and overall logistics real estate is only changing hands at incredibly high prices.
Chris Caton, Senior Vice President and Global Head of Research at Prologis, recently told Reuters that “market vacancy rates globally, we’re in the low fours (percentage-wise)… about 300 basis points below the strongest point in the last cycle.” You’re competing against every business now as they all shift to shortage and omnichannel fulfillment, often with local partners instead of their operations.
Companies with cash on hand should start to spend some of it to create partnerships and secure space. Availability will likely get tighter through the start of 2021, as many projections for e-commerce include gains in Q1. The drop-off typically seen after year-end holiday spending is likely to be mitigated by shifting consumption practices and newly ingrained habits. From the consumer perspective, it’s become just as easy to get most products shipped from a warehouse than purchased on a trip to the store. So, why change when today’s practices got them through the pandemic?
The need for emergency inventory and omnichannel fulfillment capabilities will likely keep warehouse the capacity crunch as a staple of the warehousing space until logistics-related construction catches up, which may require a broader strengthening of the economy.
Automate when available
Data-related mistakes are compounded in global supply chains. Companies should invest in as many methods as they can to eliminate these issues and audit work. One of the best places to start is by automating manual tasks.
Manual tasks can quickly bog down a supply chain and slow the movement of information and orders. Converting units and measurements, currencies, time zones, and other elements take time even for seasoned professionals. Mistakes can happen easily and often, especially in times of high stress. Automating data entry and the push/pull of information between systems can help reduce errors and intensive labor for your operations.
Verification tools can be automated to flag inconsistencies and check statuses, from manufacturing and production orders to individual shipments and document transfers. Warehouse automation is a leading contender because of the tasks it can support and analytics provided around orders, inventory, shifting consumer habits, delivery options, and improving margins.
The pandemic has pushed many consumers to adopt digital technologies faster than expected, such as mobile banking and e-commerce shopping. That’s a lesson that global supply chain professionals should take to heart, too.
Get ready for new carrier changes
When most supply chains plan for carrier changes, they think of rate increases and surcharges. These are some of the most impactful shifts for budget forecasts and understanding margins relative to demand planning. However, global disruptions have caused various carrier shifts and changes outside most risk assessment and planning.
Capacity crunches, reduced lanes, local infections, and oscillations between high and low demands have made carrier relationships challenging to maintain and their services challenging to predict. During COVID, some companies had trouble moving goods to customers and existing distribution facilities, while other supply chains were largely left alone.
The more global your supply chain, the more likely you were to be impacted. McKinsey notes that this has brought new, volatile pricing and demand where carriers will move into more sectors, such as e-commerce specific offerings and last-mile services.
All the decisions that carriers are weighing will impact your business, regardless of sector. Carriers shifting their core targets and services, those working in areas predicted to return slowly (think automotive), and changes in large-scale economic demand will reach your door. Changes to price, service type, availability, and capacity are all coming. Global supply chains need to secure reliable partners and have teams actively analyzing these market forces to help understand and predict revenue impacts.
Resiliency in global supply chains depends on your ability to create security. Redundancies for when you need them and alternative methods for localized changes are more critical than a continued push for agile and lean.
Safety, whether that comes in the form of your stock or partners or elsewhere, must become the fundamental hallmark of a global supply chain.
By Jake Rheude, VP of Marketing at Red Stag Fulfillment